Quality Maintenance In Complete Productive Maintenance
페이지 정보
작성자 Deangelo 댓글 0건 조회 4회 작성일 24-12-12 13:02본문
Continuous improvement is a fundamental principle of High quality Maintenance. Organizations should regularly attempt to enhance their upkeep processes, procedures, and practices. This includes usually reviewing maintenance information and metrics to identify areas for improvement, and implementing adjustments to improve equipment reliability and performance. Root cause analysis is another vital precept of High quality Maintenance. When equipment fails, it’s essential to identify the root trigger of the failure and take corrective motion to prevent future failures. Root trigger analysis includes identifying the underlying causes of tools failures and addressing them, quite than just fixing the immediate problem. Worker involvement is one other important precept of High quality Maintenance. Staff in any respect ranges should be involved in maintenance actions, from identifying problems to implementing solutions. Employee involvement can improve morale, foster a sense of ownership, and increase productiveness. This requires a high diploma of transparency and an understanding of the processes and work of different departments. Imagine that you simply needed to drive to Niagara Falls. Would you set out with none instructions? In all probability not, since you do not know learn how to get where you want to go. The same is true for an organization. Whole quality management requires that a company creates a strategic plan.
Also an element of these objectives are the 5S’s. They’re a set of workplace organization and cleanliness principles aimed at creating an environment friendly and productive work environment. The 5S’s each begin with the letter "S," which describe the steps concerned. 5S implementation aligns with TPM’s goal of making a clean, organized, and efficient work setting, which in flip contributes to improved productiveness and tools reliability. What Are the Six Fundamental Losses TPM Eliminates? At its core, Lean Manufacturing is about delivering worth to the shopper by minimizing waste, growing effectivity, and constantly improving processes. It originated from the Toyota Manufacturing System and has since been adapted and implemented in various industries throughout the globe. Identification and elimination of different types of waste: This includes wasted time, resources, and effort that don't add value to the end product or service. By eliminating waste, organizations can cut back costs, improve lead instances, and enhance customer satisfaction. Tradition of continuous enchancment: This means that each worker, from the highest management to the store floor staff, is encouraged to identify and recommend enhancements to the processes they're involved in. This backside-up approach ensures that the organization is continually evolving and finding new ways to ship worth to the shopper. Significance of teamwork and collaboration: It encourages cross-practical groups to work together to solve problems and implement enhancements.
4. Detail your understanding of engineering ideas and processes. 5. Include any awards, honors, or special recognition you could have received. 6. Emphasize any manufacturing or process improvement initiatives you might have led. 7. Reveal your understanding of security laws and good manufacturing practices. 8. Showcase the outcomes of any cost reduction or enchancment efforts you've undertaken. 9. Show your leadership abilities and any expertise leading teams or projects. 10. Show that you are comfy using pc software program, methods and automation controls. The three stagers were trained for higher-stage positions. A producer was having trouble maintaining with an elevated demand for orders. Pre-production lead instances have been long, and nonvalue-added administrative duties delayed orders getting to the flooring. Management turned to lean methods to map out the customer support process and remove waste from the value stream. Heijunka is a apply best lean certification course in Gujarat suited to manufacturing the place the product’s you’re making are either complex or take a very long time to create, and when the demand for your products is pretty predictable. It's because your safety stock ought to allow you to always meet an order (which won’t be true if your demand spikes randomly) and having a constant manufacturing charge is beneficial when lots of work goes into your products. JIT ("Just In Time") is one of many colleges of course of innovation focused on lowering waste.
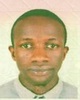
- 이전글Boost Casino: Parim Valik Eesti Mängijatele 24.12.12
- 다음글Pin Up Casino: The Ultimate Gaming Experience 24.12.12
댓글목록
등록된 댓글이 없습니다.